Aluminum alloy die-casting infiltration is a new type of casting process. The main principle is to make the foam molding model the same as the Styrofoam casting, and then immerse the aluminum alloy die-casting parts in a special refractory coating, drying and packaging. , pouring, replacing the foam model with a metal solution until the casting is produced, and then subjecting the used sand to cooling, dusting, static selection, and magnetic selection to obtain a clean, suitable dry sand, roughly referred to as white. area, red area and black area.
The main advantages of aluminum alloy die casting penetration can also be divided into three parts:
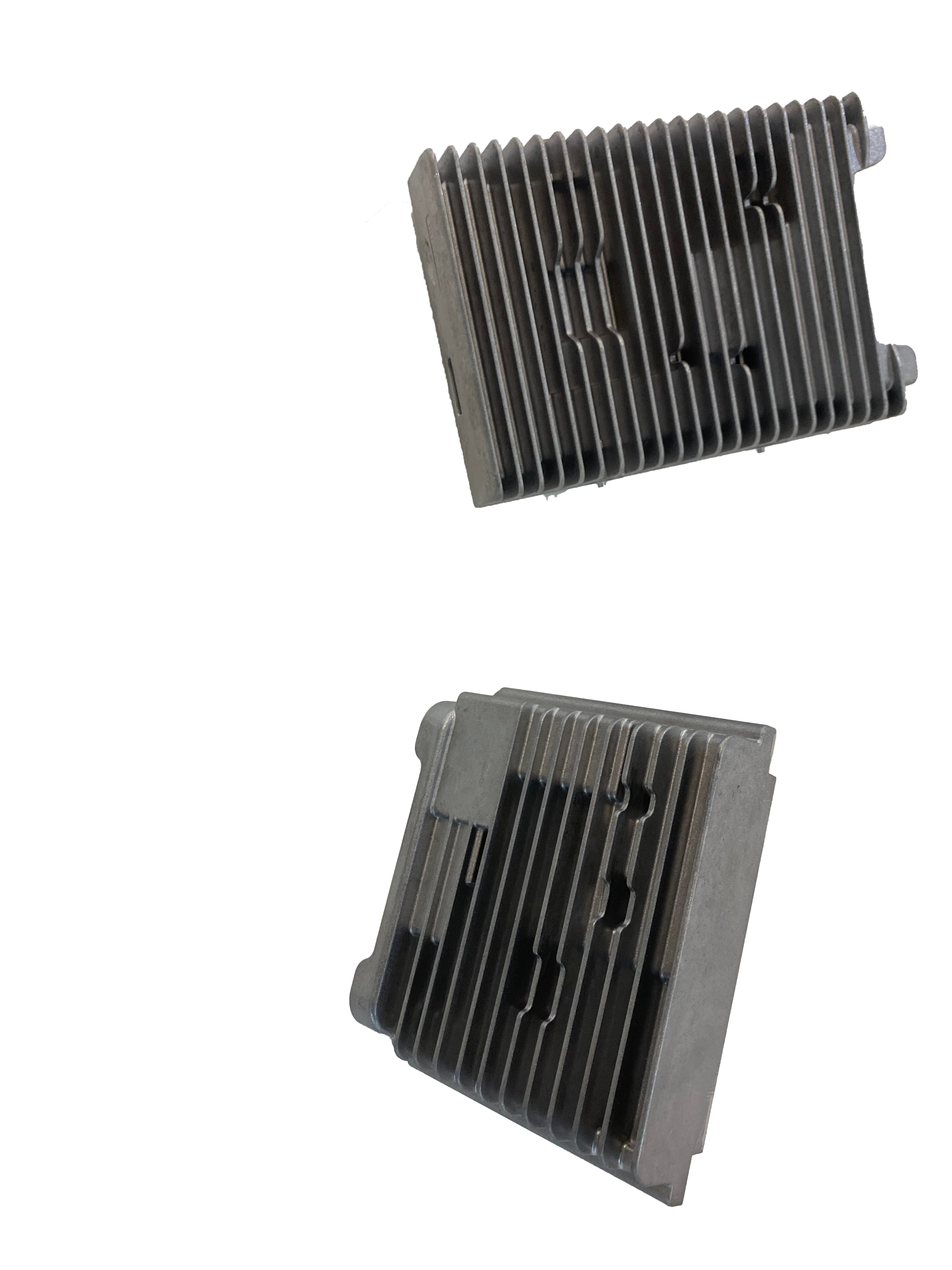
Save costs
- The mold for penetration of aluminum alloy die-casting parts can be used for life with almost no loss, reducing or eliminating mold cost.
- The dipping of aluminum alloy die-casting parts eliminates the traditional molding core process, saves manpower and reduces manufacturing costs.
- The dipping of aluminum alloy die castings has gradually developed from the foundry industry with a large number of male workers to a large number of female workers, the labor force has been greatly reduced in all aspects, and the cost has also been reduced from the workers' wages.
- The impregnated sand for aluminum alloy die castings can be recycled, with a loss of 2%-5%.
Increase efficiency and yield
- The foam model for aluminum alloy die casting impregnation is mechanical foaming. While maintaining the quality of the model, the production speed is also quite fast.
- The aluminum alloy die-casting infiltration process simplifies the cumbersome steps of the traditional process, such as the core shape, which is not only laborious but also inefficient.
- Aluminum alloy die-casting parts are dipped in one box and injected multiple times, and multiple boxes can be cast at the same time until the metal solution is used up.
Improve product quality
- Impregnation of aluminum alloy die-casting parts will eliminate defects or scraps caused by forming cores as no forming cores are required.
- No need to pack, avoid defects or debris caused by flash burrs in the box, and improve product accuracy.
- After the furnace body is discharged, most of the paint can peel off naturally without adding flash burrs. As a result, cleaning work time can be reduced by more than 50%, and cleaning costs can also be reduced.
- Since the aluminum alloy die-casting parts are impregnated with dry sand solid-type negative pressure casting, defects such as pores and sand holes in the castings are eliminated or reduced.
- Since the impregnation of the aluminum alloy die-casting part is evaporated from the foam molding model, the metal solution replaces the model, and the original shape is as close as possible to the precision casting in terms of surface finish and dimensional accuracy.
Conclusion
For more information about vacuum assisted high pressure die casting,automatic die casting machine,hpdc die casting process, please contact us at any time, we are glad to answer for you.